Have a question? Talk to our expert.
To help you navigate and better understand the world of process mineralogy and metallurgy, we've answered a few of the most popular questions.
We will continue to add to this section to ensure you are always kept informed and updated. However, should you have any questions that are not covered in this section, please don't hesitate to contact us.
Geometallurgy is defined as the practise of combining various scientific, statistical and financial inputs in order to create a predictive model for mineral processing plants and mine planning. The geometallurgical model is based specifically on key chemical, geological/structural, mineralogical, and metallurgical data. When linked to the mining plan, the geometallurgical model becomes a predictive tool for production planning. It is also used to address plant design risks related to ore variability. The unit operations of the processing plant can subsequently be modelled to obtain predictive plant output data (e.g., recoveries, tailings grades, etc.).
The following steps are followed in order to develop an effective geometallurgical program:
- Select spatially referenced, representative drill core samples, based on the geological model, for lab-scale testwork.
- Identify appropriate lab scale tests to characterize important features of the ore and perform these tests on each sample (e.g., hardness, abrasion index, mineral composition, mineral texture, flotation response, leach response, etc.).
- Model the distribution of these parameters throughout the orebody using geostatistical techniques.
- Overlay the mining plan and mining sequence plan to predict plant feed characteristics over time.
- Proactive plant .optimization

Automated mineralogy was originally conceived in the late 1980’s in order to automate the collection of mineralogical data. It consists of two parts:
- Scanning electron microscopy (SEM)
- Software controlling the data acquisition/processing
The SEM
produces a number of signals when the electron beam hits the sample; amongst others, back scattered electrons and X-rays. In automated mineralogy, we use these two signals. The back-scattered electron (BSE) signal is used in conjunction with characteristic X-ray spectra to identify the composition and abundance of elements. Back-scattered electrons are emitted from deeper locations in the sample, and the intensity of the signal is correlated with the atomic number (Z) of the mineral phase, e.g., quartz (SiO2) and galena (PbS) emit contrasting dark and bright images, respectively.
Software controlling automated data acquisition/processing
first appeared in the late 1980’s (e.g., MLA and QEMSCAN), and more recently TESCAN. The software utilizes contrasting BSE brightness levels and X-ray spectra to discriminate between different phases from a predefined mineral list. The measurement modes include modal analysis, particle mapping, bright phase searches and field mapping. The resultant data is processed via online and offline software programs to minimize the percentage of uncategorized minerals and boundary phases. Once the data has been processed and validated by chemical assays, the data is exported into a number of reports such as modal analysis, elemental deportment, mineral association, mineral liberation, mineral exposure, grain size, particle size and porosity measurement data.
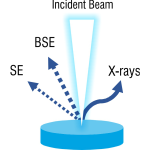
SCOPING STUDIES
Scoping studies typically include mineralogical characterization and limited metallurgical testwork. The objective of the scoping study is to examine the fundamental characteristics of the ore and understand how the ore reacts to standard metallurgical recovery processes. A preliminary estimate of achievable metal recovery is obtained. If possible, sound historical data should be incorporated. If initial testing demonstrates that the ore does not respond adequately to standard extraction processes, additional testing would be required. Scoping studies are conducted to the ±50% level of accuracy.
PREFEASIBILITY STUDIES
Prefeasibility studies (PFS) are performed for flowsheet development, and are normally conducted on representative drill core samples. The testwork includes detailed chemical, mineralogical and metallurgical analyses. The objective of the PFS is to evaluate and develop a preliminary flowsheet and to establish preliminary process design criteria, such as grind size requirements, flotation performance, leach retention times, reagent consumptions and metal recoveries. Once preliminary engineering and mine design has been completed, capex and opex calculations are performed using known unit costs. PFS studies are conducted to ±25% level of accuracy.
FEASIBILITY STUDIES
Feasibility studies (FS) or definitive feasibility studies (DFS) are conducted to a level needed to establish detailed flowsheets, material balances, process design criteria, equipment sizing and specifications. Variability composites are commonly tested to evaluate metallurgical responses that might be encountered throughout the orebody. Flotation tests will include locked-cycle tests to evaluate the impact of recirculating streams. The testwork may also incorporate bulk tests, or pilot plant tests, to generate intermediate products for definitive process evaluation. DFS studies are conducted to ±15% level of accuracy. Design and construction generally follows on the outcomes of the DFS.
A valuable metal has a certain deportment or behaviour during physical and chemical beneficiation processes. This behaviour is directly related to the mineral assemblage (composition and texture). It is therefore crucial to accurately characterize the mineralogical nature of the ore to be processed. Furthermore, specific chemical analyses and basic metallurgical tests are performed to define the deportment of the mineral of interest. The outcomes of a deportment study are used to identify possible processing options.
The following mineralogical and metallurgical tests are typically performed on the following commodities:
GOLD
Chemical assays. Modal mineralogy. Assay by size. Diagnostic leach tests. Gravity tests. Gold speciation. Gold grain association (gold carriers). Gold grain size distribution. Gold grain liberation. Gold grain exposure. Sulphide analysis: type, grain size and liberation.BASE METALS
Chemical assays. Modal mineralogy. Assay by size. Leach tests and GAC tests. Scouting flotation tests. Elemental deportment. Base metal association. Base metal size distribution. Base metal liberation and exposure. Sulphide analysis: type, grain size and liberation.PGE
Chemical assays. Modal mineralogy. Scouting flotation tests. PGE speciation. PGE grain association. PGE grain size distribution. PGE grain liberation. PGE grain exposure. Sulphide analysis: type, grain size and liberation.
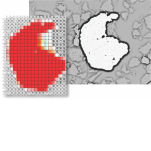
Absolutely something…
Flotation was developed in the late 19th and early 20th centuries in order to concentrate fine-grained metallic ores (mostly Pb, Zn and Cu sulphides) as gravity separation of fine-grained material was inefficient at the time. Although other applications were tested in the 1920’s and 1930’s (e.g., coal cleaning, phosphates and potash), base metal sulphide ores have remained the dominant application in the mining sector throughout the 20th and 21st centuries. This was accomplished by advancements in flotation technologies, which saw sulphide mineral collectors (e.g., xanthates) replace bulk flotation oils and other outdated methods (e.g., ‘skin’ flotation, which relies on the surface tension of water).
In addition to base metal sulphide ores, flotation is used to concentrate a number of other commodities, such as gold, silver, PGEs, molybdenum, mercury, antimony, fluorspar, tungsten, tantalum, tin, lithium, silica, base metal oxides, barite, coal, graphite and oil sands. Alternative applications include the removal of organic material and other pollutants from water, the removal of particulates from food processing plants, the removal of solids after AMD neutralization, treatment of effluent, paint manufacturing and paper recycling (deinking).

Fire assay is an accurate (but destructive) technique used for the quantitative determination of precious metals such as gold, silver, platinum and palladium. Although the technique is time consuming in comparison to modern analytical methods, this aspect is compensated by the ability to assay hundreds of samples per day. The technique can be summarized into 3 parts:
FUSION
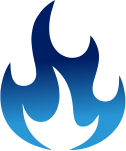
The sample is mixed with a carbon source, one or more fluxes (e.g. litharge) and a collecting agent (e.g., lead) in a refractory crucible and loaded into a furnace for about an hour at 1150 °C. This produces a heavy metallic alloy and a glassy slag. The mixture is poured into a mould, where the metallic alloy sinks to the bottom and forms a ‘button’. Once cooled, the ‘button’ is knocked out for cupellation.
CUPELLATION
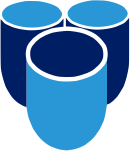
The objective of cupellation is to separate the precious metals from the collecting agent. The button is loaded into an oxidizing cupellation furnace at 1000 °C. The collector (commonly lead) melts, oxidizes to PbO and is then absorbed by a porous crucible (or cupel) made from bone ash or magnesium oxide. The remaining precious metals are left behind in the form of a metal prill.
ANALYSIS
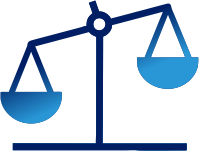
Prior to analysis, the prill is treated with an acid (e.g., nitric or sulphuric acid) to remove the silver. Thereafter, the precious metal content can be determined by gravimetric or instrumental finishes. The former utilizes a microbalance and is typically used when samples are high grade. The latter finish employs aqua-regia digestion and analysis by ICP-OES/AAS.